The Art of Block Printing and Wooden Printing Blocks
Block printing is an art technique of printing that has its roots in ancient history. It’s a creative mode of printing beautiful patterns, designs, and colors on the surface wherein the image or motif is traced and carved on wooden printing blocks by a craftsman. The art of Block Printing is a printing technique or process that has survived somehow from the past to this age.
Table of Contents
What is Block Printing?
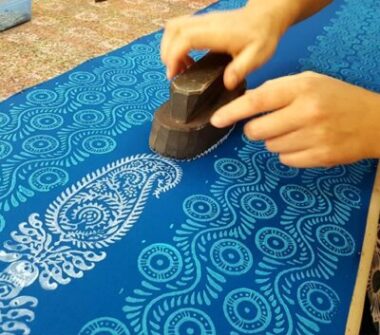
Block Printing is a printing process for printing text, images, or patterns as the simplest way of printing on textiles, paper, clay, etc… Block printing is also a conventional kind of fabric printing technique that’s still used extensively. it’s an easy and instantaneous printing technique that produces rewarding results on fabric and paper. In essence, block printing is the same as rubber stamping, with many of the printing skills being transferable. Block printing is additionally an incredibly creative process. With only 1 wooden printing block you can create endless block printing designs and variations on a subject, and become a fabric designer.
Block Printing History
As the simplest way of printing on cloth, the earliest surviving examples from China date to before 220 AD. Block printing existed in Tang China during the 7th century AD and remained the common method of printing books and other texts, also as images, until the 19th century, in East Asia. Ukiyo-e woodblock prints are the best-known form of Japanese woodblock art print. ‘Woodcut’ is also an art form like block printing in Europe, it is a technique for printing images on paper, apart from the block books produced mainly within the 15th century in India. There are claims by several countries having block printing originated/developed in their country but several pieces of evidence are found in India from ruins of ancient civilizations that date from thousand years. as an example Scraps of clothing found within the ruins of Mohenjo Daro, provide evidence that block printing on fabric was practiced in India in 3000 BCE. Since the 12th century, the art of Block Printing flourished further with the receivable of royal patronage. Rajasthan and Gujarat became important centers of Block Print art. Today Block Printing has reached new heights by making it to various corners of the planet.
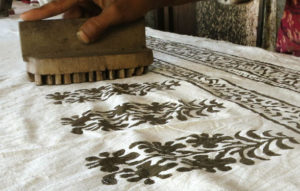
How to do block Printing on fabric
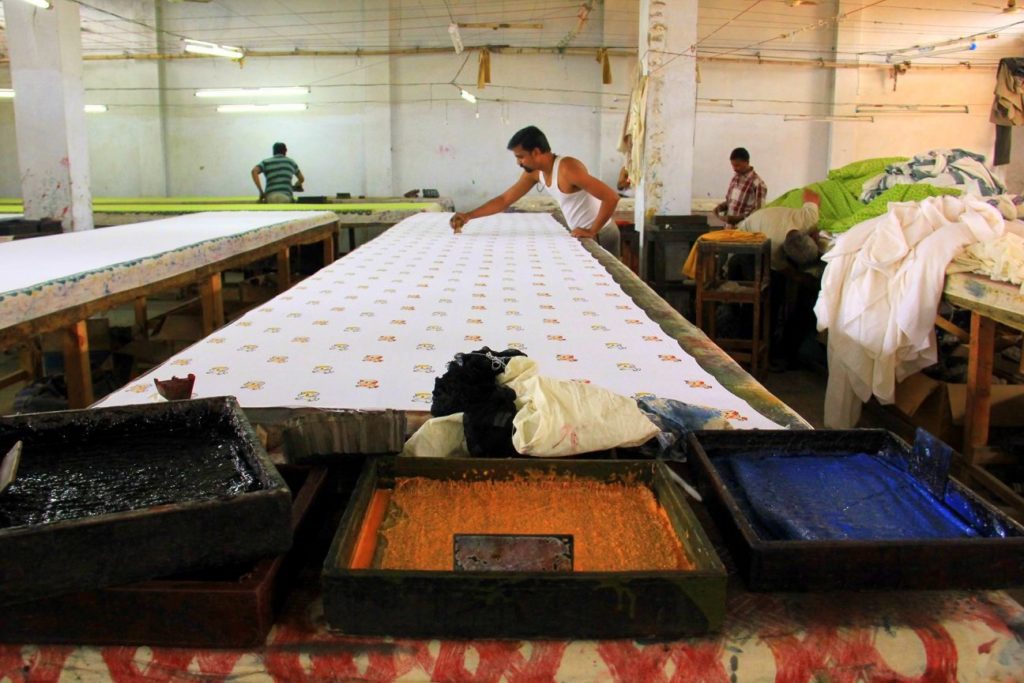
Block printing may be a typical process and takes time. The printers use 2 or 3 or sometimes more wooden printing blocks to complete a design. The method of block printing begins with wooden printing blocks. Woodcarvers carve designs into wood planks/blocks. The back of the wooden printing block is fitted with a handle for the printers to hold it. The next step within the method is the arrangement of the fabric. Workers lay down several layers of jute over a rectangular table. The jute may be a pad to produce resiliency to the printing surface. Printing starts from left to right. When the printer dips the printing block into the dye/color and then presses it onto the material, the printer slams the rear of the printing block hard with the fist to make a clear impression. Then the printer moves the printing block to the subsequent portion of the material to be colored.
The printers also pull a wooden cart carrying their wooden printing blocks, while they print. The wooden printing blocks are changed to create different patterns depending on the pattern or style. Custom designs and unique colors are often used from one fabric to another, creating new styles or patterns. Each color of a design is printed by a separate printer, coming behind the one before. The method requires teamwork, as each subsequent printer must place the block accurately to form a stunning, whole pattern. After the printing is complete on the complete length of the fabric, it is treated to fix the dyes. This technique of ‘block printing’ has been used for hundreds of years and remains in practice. If you want to try this art of block printing, you can buy wooden printing blocks at https://www.rrprintingtools.com. The blocks available here are smaller and simple to use.
Types Of Block Printing in India
Here are the ten Block Printing/ Fabric Dyeing Techniques of India:
1. Bagh Block Printing
The origins of the Bagh block printing are uncertain, but the belief is that it is over 1,000 years old, with the technique handed down from generation to generation. This art traveled with settlers from Jawad in the Madhya Pradesh state in India or from block printers of Rajasthan state. Another theory is that the Chhipas (or traditional cloth printers), a Muslim Khatri community, that does Bagh block printing, traveled around 400 years ago from Larkana in Sindh province, Pakistan, which is believed as the origin of the Arjak block printing. The reasons for the migration are unclear, but the Bagh river, which provided the water necessary for the laundry of cloth and processing of vegetable dyes, can be the first reason for settling in Bagh. Additionally, the mineral contents in the water of the Bagh river enhance the dyes, giving them a luminous quality. It gives Bagh print an advantage over other printing techniques in Madhya Pradesh and Rajasthan regions.
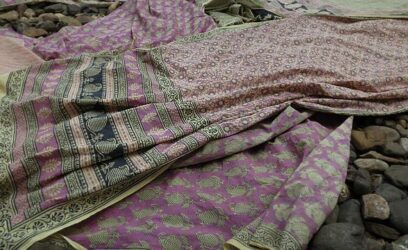
In the 1960s, many printers abandoned the traditional process of Bagh block printing because of synthetic fabrics. However, some printers continued to practice the conventional technique and brought Bagh block prints to international prominence. In 2011, a garment made with the Bagh block print technique was showcased during a tableau theme of the Madhya Pradesh state at the Republic Day parade in New Delhi on 26 January 2011. A Shalbhanjika, the celestial apsara of the 11th century, got featured in the Parade and was draped in Bagh printed clothing.
2. Kalamkari Printing
The word ‘Kalamkari,’ is derived from the word ‘Qualamkars’ (the practitioners of this craft). In ancient times, groups of singers, musicians, and painters, called ‘Chitrakattis,’ moved from village to village to tell stories of Hindu mythology. Like the illustrations found within the Hindu temples (large panels of kalamkari depicting the episodes of Indian mythology, stained glasses of the Christian cathedrals), they illustrated their stories using large canvas, painted on the spot, with dyes extracted from plants. As a sort, it found its peak within the wealthy Golconda sultanate, Hyderabad, during the Middle Ages. This craft within the Coromandel and Golconda provinces received royal patronage from the Mughals, and the practitioners of this craft were called “qualamkars.” ‘Kalamkari Printing‘ had a decline, but later it was revived in India and abroad for its craftsmanship. Since the 18th-century British people likes it as an ornamental element for clothing.
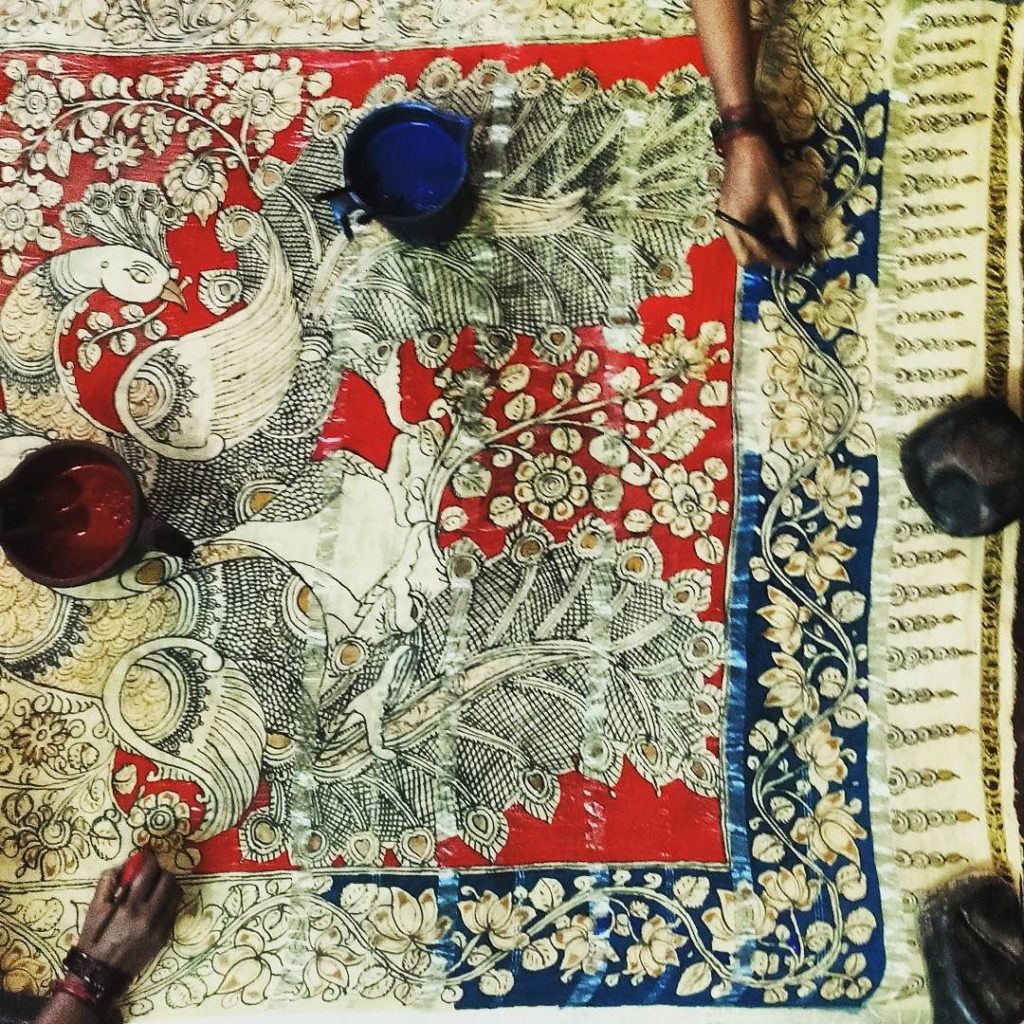
Origin of Word KALAMKARI:
Kalamkari is from ‘Kalam’ (pen) and ‘Kari’ (craftsmanship). These words are Persian words that mean the art of hand painting done on fabrics with the employment of a pen. It later got extended to include hand block printing and utilized wooden printing blocks for printing. Within the craft Kalamkari, a pointy bamboo stick padded with hair or cotton and tied with string on one end to manage the flow of color, is known as pen. Hand-drawn painted wall cloth in natural colors that include giant tapestries to small squares were the outcomes of the art of Kalamkari. These cloth paintings filled with characters and storyboard narratives have freshness about them.
3. Ajrak Block Printing
Though Ajrak garments are worn by ladies mostly, not many understand the origin and history of this traditional ethnic art. According to researchers, Ajrak block printing art belongs to the ‘Khatri’ community. A community that resided near river Sindh in Pakistan.
Ajrak Goes to Kutch:
In the 16th century, numerous Ajrak printers moved to the Kutch region, invited by the King of Kutch, who was passionate about the art. Ajrak flourished in Kutch and started to be related to the Maldharis in the region. This art technique remained unchanged until the commercial Revolution began penetrating the villages. In the 1940s, the introduction and demand of synthetic fabrics and vibrant chemical colors dwindled the popularity of Ajrak for nearly 15 years. Fortunately, the persistent efforts of some patrons and printers helped revive this block printing art within the 1960s. ‘Ajrak’ is an Arabic word that means ‘blue.’ Word describes a cloth that is highlighted primarily with dark indigo and delightful crimson (red) colors. But one can also notice hints of black and white on the material used for highlighting the classic geometric patterns. Ajrak could be a mere block printing technique utilized in Sindh, but also you may notice some men adorning Ajrak turbans and ladies wearing Ajrak shawls in this region.
Hows was Ajrak created? Ajrak is a type of block printing technique that incorporates a reference to the Sufi culture that dominates the Sindh region. That’s why there are numerous Ajrak makers near the sacred shrines within the interior parts of Sindh.
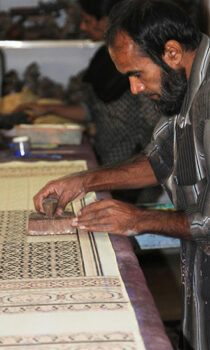
There are usually 4 main themes used in the Ajrak block printing technique:
- Teli Ajrak block printing
- Do Rangi Ajrak block printing
- Sabuni Ajrak block printing
- Kori Ajrak block printing
The steps in making Ajrak print:
- ‘Churrai’ or Fabric Washing: “Churrai” is a method of cleaning the fabric. The fabric is first washed and beaten to get rid of all dirt and impurities. This is often followed by the soaking of the fabric in a very special solution of soda bio-carbonate and oil. This can be a rather complex process and should take a pair of days.
- Block Printing: Block Printing is that the next step within the Ajrak-making process. The printers print real Ajrak on either side of the fabric. This is also a kind of “resist printing”. Ajrak printing is completed manually using wooden printing blocks.
- Bleaching: Finally, the Ajraks bear another washing process with water, soda, and bleaching agent. This last step lends a stunning vibrancy to the material colors.
The Popularity of Ajrak block print.
Ajrak block printing has one outstanding feature, it showcases a mix of resist printing and dyeing techniques on one fabric. Skilled printers perform the process on either side of the fabric with sheer consistency. Ajrak block printing uses the mud-resist technique in several stages of the printing. Ajrak block printing was done majorly on lungis and turbans, in the past, but now printers are using this method to make stunning silhouettes such as kurtas, scarves, dupattas, skirts, and pants. You may also find beautiful ornamentation on Ajrak garments like gota and sequence work. It’s truly amazing to witness the innovative revival of Ajrak art within the previous couple of decades. We highly recommend researching this trend if you are a lover of ethnic fashion!
4. Dabu Block Printing
Dabu print is an ancient hand-block printing technique, that originated in the lands of Rajasthan. Dabu print fabric has its own charm and wonders that are recognized around the world. The practice of Dabu print almost died within the last century; but it had been revived by artisans and today, it’s a flourishing business across the world. Dabu printing could be a labor-intensive task and requires several steps in the printing and dyeing procedure. Dabu printing may be a mud-resisting form of hand-block printing. The final Dabu print on fabric looks very like Batik, but the technique used is totally different. Dabu print may be a combination of highly skilled labor and delightful motifs. Artisans tend to provide traditional and classic prints that are considered authentic. Dabu printing could be a slow process but it yields artistic results. Rajasthan being the house of the Dabu printing technique, the motifs used have a conventional approach to its existence. Dabu print uses natural dyes which makes it environmentally suitable. Lots of labor and extensive struggle are required to form Dabu print fabric.
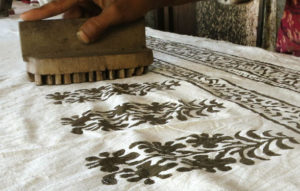
Process of making Dabu print fabric is so prolonged that the end result is worthwhile. Plain fabric is first washed to get rid of any impurities, which can interfere the dyeing process. Designs are then hand printed on the material using blocks dipped in fast dyes. After this, mud resist is employed that produces this print so unique. After printing is finished, the Dabu print fabric is spread within the sun, where it dries out. Next, the material is dipped in vat of dye, dried again and at last washed thoroughly to get rid of excess dye. Parts of the material that are uncovered with mud resist are of various color than the remainder of the material. MOTIFS and styles. Motifs on Dabu print fabric are picked from nature and its surrounding elements which include peacocks, mangoes, leaves, sunflower and animal figures. Wavy lines, dots and various geometric shapes are used. These motifs are then crafted on wooden printing blocks. Final design is repeated again and again everywhere the material. Often, the mud paste cracks and leaks, that makes veins the same as Batik.
5. Gold and Silver Dust
Traditional Khari printing is the process of printing fabric with the dust of precious metals with motifs patterning them with the sparkle of gold and silver. Simulating the design of the high-priced Zardozi metal thread embroidery, the age-old printing remains identical though the utilization of valuable dust has been largely substituted by crushed mica – chamki and other cheaper metal dust.
While block printing is a fabric printing process but the Khari printing process is a surface embellishment process and it doesn’t permeate the textile. Though originally printed on different kinds of cotton or silk, the flexibility of the printer now extends not only to the wide selection of textile fibers now available but to paper in addition.
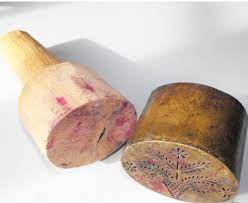
The process starts with the specially prepared Roghan gum paste manufactured from a cooked mixture of purgative that has been processed through repeated boiling till it forms a thick, viscous, gooey mass. Followed by the addition of other ingredients that include turpentine, further heated, thickened, and strained till the paste achieves a suitable printing consistency.
The stamping tools employed in Khari printing also are different from other types of block printing. An ingenuous system it uses two different blocks, close fitted into one another, rather a sort of glove. The outer sancha metal case is manufactured from brass and looks to be printed perforated onto the surface of its base. The sancha could be of any shape round, square, or any that’s suitable for the aim. The inner component of the sancha is the Hatha wooden mallet, fitting perfectly into the metal sleeve. The Hatha works as a plunger. Operating on a principle like an extrusion used for savories or pasta, the Hatha forces the thick viscous roghan paste through the perforation to create the motif on the textile. this can be only the primary introduction to printing. Metal powders or mica abrakh powders are dusted on, adhering to the roghan paste, before the paste sets. When dried any excess powder is removed and saved for further use, while the glittering textile is prepared to be used.
A wide range of motifs is created, the sole constraint in Khari work being that the patterns are fashioned of smallish dots and dashes as long and heavy lines or filled motifs stiffen the surface reducing drapability. The finished product replicates the posh metal thread embroidery. The finished product replicates metal thread embroidery.
6. Sanganeri Block Printing
Sanganeri Printing is a hand-block printing technique originating from Sanganer, a village within the southern part of Jaipur, Rajasthan. this way of textile printing is sort of 5 centuries old and to date holds a prominent place within the world of printers and craftsmen. Delicate patterns and contours with vibrant colored designs are the defining factors of this type of printing technique. The Sanganeri block printing came into existence between the 16th and 17th centuries. It became one of the main export items for the East Indies Company, and its trademark was the first dye used for printing designs. This dye soon became a matter of significance in European culture still. Royal patronage and heritage-inspired the good cultivation of this art, which has been around for years and is nearly as old because of the country itself. Rich traders and royal families have propagated this art and its influence has spread far and wide into the basic nature of Indian tradition and culture. The dyers originally belonged to a community called the ‘chippa‘ community. The bulk of them are Muslims. The foremost interesting fact is that the entire family, including children, gets entangled in the process. Today, nearly 3000 people are employed in practicing this craft on an expert level. There is a good variety within the forms of designs and patterns used in Sanganeri print, which incorporates every kind of flower motif, most ones being of sunflower, roses, and narcissus’. except for flowers, designs depicting various gods, fruits and folk scenes are popular. The simple and artistic variety of this block printing technique makes it popular amongst all age groups. With the passage of time and advancements, dyers have started experimenting with unusual color combinations. Overlapping colors like red and pink, or purple and orange isn’t very uncommon nowadays.
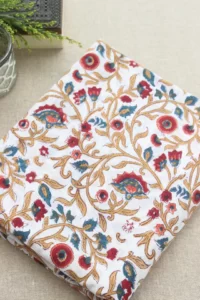
7. Bandhani Printing
The Bandhani, is dying technique created by the Indian dyers’ community. It requires a lot of patience, and talent and is labor intensive. This art has influenced numerous cultures and regions and hence its origin is uncertain. it’s known as Sungudi in Tamil Nadu(India), Shibori in Japan, and Plangi in Malay. But this art originated in Sindh. In the present day, Bandhani is prevalent in Gujarat, Rajasthan, and Madras. Rajasthan’s leheriya pattern often called the road pattern, is exclusive to the state. Bandhani is thought of as Sungudi in Madras. While the final printed products look similar, the method involved in making them is widely different. Bandhani comes from the verb Bandhana, which implies to tie. Resist-dyeing is involved where certain areas of the fabric are tied to guard them against getting dyed. The tie-dye is done in two steps: tying and dyeing. The tying is often done on four or six layers of cloth and is then printed with designs.
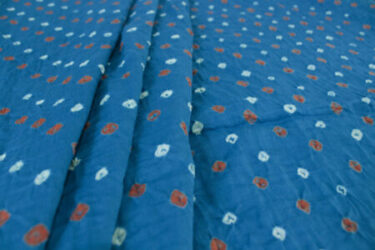
Wooden Printing blocks, nail blocks and paper patterns are used for printing. A paste of geru and water is employed in the writing. Tying is finished using twisted cotton threads of varied thickness. Fine patterns are created using fine threads while thicker threads are used for bold patterns. Both square and circular dots will be formed through tying. The square patterns are created by flattening the material during a square and picking the pointed corners for tying. The round dots are produced by twirling the material and tying it with thread. Traditionally natural colors are used for dyeing fabric. The components used for natural dyeing are rusted iron pieces, myrobalan powder, alizarin dye, kesuda flowers, pomegranate peel, dried mango powder, juice and alum. To read more about Bandhani Printing clicks on hyperlink.
8. Leheriya Printing
Leheriya (or leheriya, Lehariya) may be a traditional kind of hand dye practiced in Rajasthan, India that ends up in brightly colored cloth with distinctive patterns. The technique gets its name from the Rajasthani word for wave because the dyeing technique is usually accustomed produce complex wave patterns. Lehariya is distinguished by the natural, ripple effect in mesmerizing colors, employing a color-resist dyeing technique. The wavy, diagonal stripes created through this system look bewitching in brilliant color combinations. The leheriya was patronized within the nineteenth and early twentieth century by the local traders and merchants who wore turbans of bright Leheriya fabric. The material is rolled diagonally and certain portions are resisted by lightly binding threads at a brief distance from each other before the material is dyed. If the space is shorter, then greater skill is required in preventing one color from spilling into the opposite. the method of dyeing is repeated until the requisite number of colors is obtained. The Leheriya could be a visual invocation of the flow of water.. creating a peaceful and restful coastal feel. Leheriya dyeing is completed on thin cotton or silk cloth, usually in lengths appropriate for turbans or saris. According to World Textiles: a visible Guide to Traditional Techniques, the material is “rolled diagonally from one corner to the alternative selvage, then tied at the specified intervals and dyed”. Traditional leheriya employs natural dyes and multiple washes and uses indigo or alizarin during the ultimate stage of preparation.
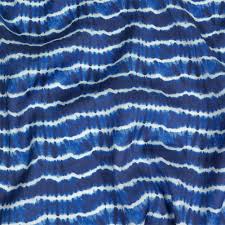
9. Mothara
Dyeing a leheriya printed fabric again using the same technique produces mothara. within the making of mothara, the first resists are removed and therefore the fabric is re-rolled and tied along the alternative diagonal. This ends up in a checkered pattern with small undyed areas occurring at regular intervals. The undyed areas are about the scale of a lentil, hence the name mothara (moth means lentil in Hindi). An ancient and ever popular technique, tie-dye may be a process of resist dyeing textiles typically using bright colors. While there are several variations in technique, the strategy basically involves patterns of color by folding, tying, stitching, crumpling the material to inhibit the flow of the dye into the folds of the material. The pattern of the folds and where the colours are squirted determines the ultimate design. Several variations of the tie-dye technique are evident the globe over, from the Shibori in Japan, the Hausa technique in geographical region, Plangi and Tritik in Indonesia to the gorgeous Bandhani, Ikat and Leheriya patterns of India.
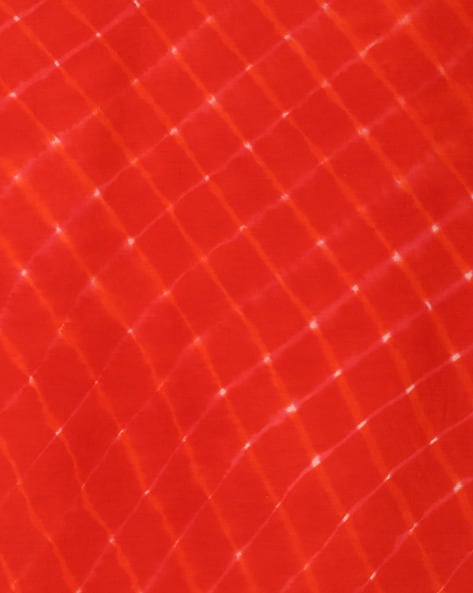
10. Batik Printing
Batik printing is a method for printing designs on fabric with wax resist. In Japanese tradition, wax is employed to color the fabric which is bathed in dye afterward. The result’s a fabric tainted with the color of the dye except on parts where there’s wax. What makes batik printing look cool is that some areas will appear to own cracked lines. Batik masters are known for making more complicated designs through the layering of dyes. Batik printing is a good way for printing fabric. You’ll be able to choose the color of the fabric, but light colors would yield better results. you’ll choose one or many colors of dye to use for the printing. More colors give more fun outputs, but one color is additionally interesting. To try batik printing, you may need a plain fabric, some warm water and detergent, batik wax, dyes in your chosen color, a tambour, tjanting tools, and a tub. Batik printing starts with washing the fabric with warm water and detergent. this is often to get rid of impurities that may affect the fabric. Afterward, the fabric is soaked within the base color. this is often the color that will show on the waxed places since later dyeing won’t show on them anymore. This step is skipped if the required output has white waxed areas and different colored batik regions.
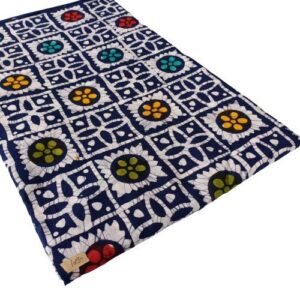
The fabric is stretched on a frame to form designing the print easier. Designing the fabric can now begin. Tainting tools are traditionally used for printing with wax on fabric. Different tainting tools can be utilized to print thicker or thinner lines to make variations in the pattern. Once the printing is finished, the fabric must be washed in warm water and detergent again before it goes through different dyes. If you plan to use quite one color, start with the lightest. To read more about Batik Printing click on the hyperlink.
11. Bagru Block Printing
Bagru printing may be a traditional printing technique that’s done using natural colors. It’s a craft practiced by the ‘chippas’ community in a remote town of Rajasthan, Bagru. Bagru Printing is mostly done on a blue or indigo background. This region is popular for 2 sorts of prints: Dabu prints and seyali-bagru prints. The seyali-bagru printed fabrics are known for their characteristic black and yellow ochre/cream color combinations. Dabu prints, on the opposite hand, are created employing a special resist technique (hiding the print from dye). The patterns and motifs predominant in traditional Bagru prints were geometrical (circular) but were combined with bird, animal, and floral forms to make beautiful designs.
CONCLUSION
All the printing techniques including tie and dye, and block printing that are practiced in India are the result of the rich culture and heritage of the country. Creativity, craftsmanship, and a full lot of effort get into keeping these printing techniques alive and trending around the globe. This huge collection of printing techniques and designs contributes to the popular saying “unity in diversity”. The variety of these intricate designs and various colors may be a rich source of culture that has been passed on from generation to generation within the country. They deserve all the patronage and love that they get.
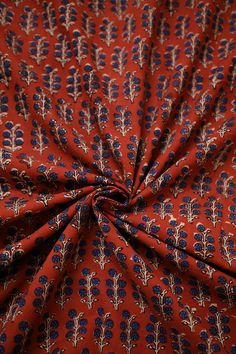
The Art of Wooden Printing Blocks
Block printing is one of the oldest art techniques of printing which has its roots in ancient India. And Wooden Printing blocks are a creative mode of block printing beautiful patterns, designs, and colors on the surface; wherein the image or motif is traced and carved by hands on these blocks by a craftsman. Wooden printing Blocks are a kind of stamps, similar to rubber stamps, made out of Sheesham wood. Printing with wooden printing blocks has its origins in India as old as 500 years ago! With the arrival of your time and technology, this ancient technique started spreading widely in Northern India, and now almost 80% of Indian houses have some or the opposite thing which has block printing done on that with wooden printing blocks. Be it on bed covers, cushion covers, table covers, or lamps; these block printing designs leave a mark on the viewers’ eyes. The best part about wooden printing blocks is, they’re completely eco-friendly and have no damaging effects on fabric or canvas or mother nature. They do not require any artificial substance, and hence it’s counted as one of the purest varieties of handmade crafts. Sheesham wood is used for making wooden printing blocks which is entirely nature’s gift and thus has no harmful effects. Wooden printing Blocks are available in an exceedingly vast sort of designs. The printing designs are vivacious and lively. For one model there are numerous, and for single colors, there are numerous designs. Wooden Printing blocks also are referred to as buntas, buntis, pur, Biba, or bibal and are made of well-seasoned Sheesham wood. Wooden Printing blocks, copper blocks, cast metal blocks, and nail blocks are the four used types of printing blocks. Each block has its own merits and demerits and is employed in accordance with the pattern to be printed. The copper and brass blocks are ideal for printing intricate and dotted designs. It also said, this method dated back 2 thousand years and originated in China. it’s one of the methods for printing in East Asia. Initially, this method was used for printing on fabric by applying the block on silk fabric and applying pressure to make sure that the design gets transferred to the fabric.
The Origin Of Wooden Printing Blocks
Printing has its origins in India! In ancient times, there was no source for vivid colors, designs, and patterns and hence, our distinctive craftsmen used natural dyes(mineral and vegetable dyes) and created wonderful patterns in the type of wooden printing blocks. The traditional style of printing involves numerous varieties of wooden printing blocks and also the extraordinary talent of the artisans. Since 3000 BC, Wooden Printing blocks are being used in India, although no such blocks or textiles carrying their imprint have survived the ravages of your time. Some scholars believe that India is the birthplace of printed textiles. Another school of thought contends that, since China was the primary country to manufacture printed books, they may have invented wooden printing blocks and traces its origins to 700 A.D. China. The Chinese introduced innovative solutions for printing using carved wooden printing blocks. It promoted the recognition of block printing methods. Here one design was used on a block and then used either on fabric or paper. Wooden Printing Blocks were used to print religious literature on a large scale. The famous book published using this method was Diamond Sutra which originated within the Tang dynasty. It had images and text about Buddha and helped to function as religious literature to market the faith within the region. Even before Europeans mastered the art of printing employing a press, the Chinese introduced a variety of printing that used hand-carved wooden blocks. this method used paper and ink (both of which originated in China itself). this method was inspired by the concept of using carved wooden printing blocks (originally from Mesopotamia). Slowly and gradually, the identical was popularly mentioned in other parts of Asia, and hence the art of block printing on fabric gained popularity. India too uses the technique to urge the famous Bagru prints on the fabric that uses wooden printing blocks and locally sourced dyes. this system is very simple and sustainable. These blocks are often used for an extended time and are affordable.
On the idea of material used to manufacture a printing block, they're classified into four categories and serve distinct purpose.
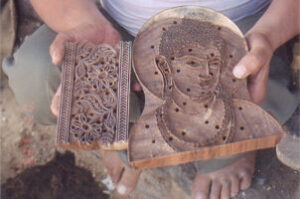
Wooden Printing Blocks
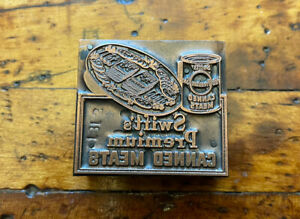
Copper Printing Blocks
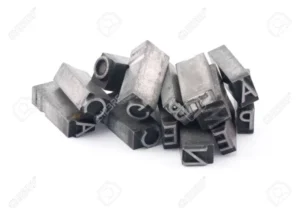
Cast Metal Printing Blocks
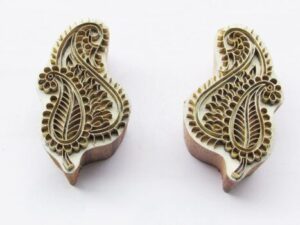
Brass Printing Blocks
Further Wooden printing blocks are classified into three categories as Rekh, Gadh and Datta on the basis of their usage.
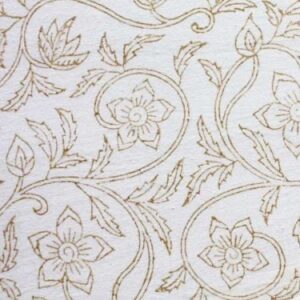
Rekh or Masa:
Rekh are used to print outline design and are craved depending upon the form of the designs needed. They are the primary wooden printing blocks to start printing and is a guide for the position of subsequent blocks. Since these blocks are the first blocks, they have to be carved intricately and even.
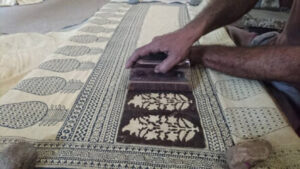
Gadh or Kappu:
The function of Gadh wooden printing blocks is that the polar opposite of Rekh blocks. These blocks are employed to form colours within the background of the fabric.
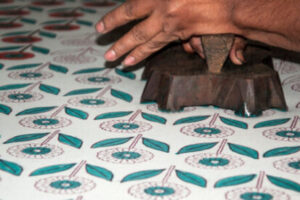
Datta or Tapki:
The filler blocks are called Datta wooden printing blocks and that they are curved in bold relied betting on the colors employed in the designs.
How Wooden Printing Blocks are made?
The best part about this method of printing with wooden printing blocks is, it’s completely eco-friendly and has no damaging effects on fabric or canvas. they do not require any artificial substance, and hence it’s counted jointly as the purest forms of handmade crafts. Sheesham wood is utilized for creating wooden printing blocks which are entirely nature’s gift and then have no harmful effects. The first step is to draw the motif on woodblock/plank. Once the design/motif has been approved and ready for carving, a wooden block/plank is prepared by hand sanding and coating the surface with a white paste so as that the surface is uniform and smooth for imprinting design thereon. Then the design or motif is imprinted on the woodblock for carve. Carvers then chisel out the empty space from the woodblock that the design/motif remains along the printing surface. this could be done by hand using very small chisels. It is a labor-intensive process that needs skill, experience, and patience. the finished blocks are checked for accuracy and soaked in oil to cure the wood so it doesn’t crack and enhance its life, and are then able to be employed in printing. The result? Beautiful textiles for a living!
Tools for making Wooden Printing Blocks
At every stage of the process of making wooden printing blocks, a definite tool is required for the designs to be carved. All of these tools are still operated by hand, and no machines are employed. the variability of tools utilized in making wooden printing blocks are listed below:
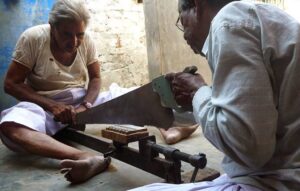
Cutting Tools
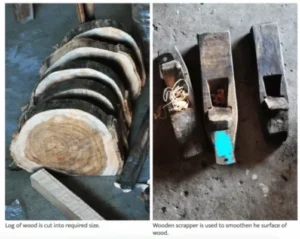
Smoothening Tools
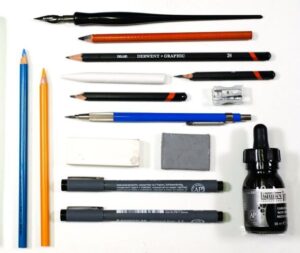
Drawing Tools
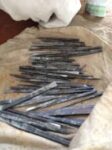
Carving Tools
Wooden Printng Blocks-making process
- Purchasing wood: Buying the wood is that the first stage in block making. Sheesham is that the best wood for carving intricate motifs since it’s less liable to flaking and cracking.
- Preparing the wood: The wood is now turned into smaller pieces and seasoned, scrapped employing a plane to urge a smooth finish. The logs are then washed with Riverstone, sand, and water to allow the woodblocks a glossy finish. The woodblocks (kaplo) are applied with wet balls of khaddi (white chalk made by block-makers) which leave a white covering on the block.
- Designing: Before the khaddi dries out, the designs are sketched symmetrically on paper and then pasted on the woodblock. The logs are then left to dry in the sun.
- Carving: Carving is the most time-consuming process and takes about three weeks to finish. The traced designs are carved using different chisels. Firstly, the large designs are engraved. After that, the holes are made and greater unwanted portions are removed. Once the surplus wooden particles are removed, the block-makers target achieving a more refined appearance.
- Finishing: This is the ultimate step within the wooden printing blocks production process. Handles are affixed to the blocks to make them easier to manage. Each weaving family has its own handle that may be used to identify who carved the block. Subsequently, air holes are drilled to permit trapped air to flee. If otherwise, air bubbles will cause smudging and spreading of the color while stamping. The wood is seasoned and soaked in mustard oil for 10-15 days. Finally, impressions of the block are stamped on waste cloth or paper to confirm that they’re accurate and precise.
Every Wooden printing block is distinct and holds a special place in the history of art and culture. As torchbearers of India’s rich cultural legacy, it’s our obligation to honor, safeguard, and nourish these crafts. RR Printing Tools takes tutelage in ensuring that these beautiful patterns are cherished. you’ll be able to find our collection of lovely wooden printing blocks on our website.
How to clean Wooden Printing Blocks??
Using anything from a straightforward vinegar and water solution or a light dish soap together with warm water can make all the difference. You can also use your regular multi-purpose detergent, albeit diluted with water. Although, you can’t bleach off using the cruel chemicals away on these blocks because it will cause the wood to dry out.
Here are some steps that you simply need to follow:
- Take a bucket with water and use it to dip the dirty blocks.
- Once you scrub the block, then immediately dip it in another vessel that has clean water.
- You can then wipe these clean employing a dry cloth.
- Place these under shade to dry completely.
Shop for Wooden Printing Blocks
If you are looking forward to buying wooden printing blocks, then RR Printing Tools presents you with beautiful sets of Wooden Printing Blocks for helping you to bring out your creativity. You can check out the full range at the shop page https://www.rrprintingtools.com/wooden-printing-blocks/ .Your preferred designs get carved on a piece of a wooden block. We also offer Custom Carved Wooden Printing Stamps to our customers. Please feel free to reach us and know more about our product range.